In celebration of Earth Day, we’re proud to share that Evoco and Bared reach over 1 million footwear components made together.
Continue readingEvoco CEO, Jason Robinson, recognized as Fasken Climate Tech Founder of the Year
Evoco’s Co-Founder and CEO, Jason Robinson, named as Fasken’s Climate Tech Founder of the Year for 2024.
Continue readingEvoco Joins the Renewable Carbon Initiative
Evoco Ltd., A powerful materials innovation company at the forefront of plant-based science, is joining the Renewable Carbon Initative, working to shift to a defossilized future.
Continue readingA Shared Vision for Sustainable Innovation: L’Oréal Canada’s Visit to Evoco
Evoco Ltd., A powerful materials innovation company at the forefront of plant-based science, is pleased to announce our renewal of GreenCircle Certification on Earth Day for 2024.
Continue readingDesigning Comfortable and Sustainable Footwear: Exploring Insole Material Innovations
Designing Comfortable and Sustainable Footwear: Exploring Insole Material Innovations

In the world of footwear design, selecting the right insole material is crucial for achieving optimal comfort and support. With a wide range of options available, it’s important for footwear designers to make informed decisions that align with their design goals and the needs of their target audience. In this article, we will delve into the crucial factors to consider when selecting insole materials.
Factors to Consider When Choosing Insole Material:
Footwear Type: The specific type of shoe or boot being designed will heavily influence the choice of insole material. Different activities and usage scenarios require different levels of support and cushioning.
Activity Level: Consider the intended level of activity for the footwear. Insoles for high-performance athletic shoes may require enhanced shock absorption and stability, while casual or everyday footwear may prioritize comfort and breathability.
Material Properties: Each insole material offers unique properties that impact factors such as breathability, moisture-wicking, odor control, and overall comfort. Evaluate these properties based on your design goals and the needs of your target audience.
Price Point: The cost of materials is an important consideration, as it can affect the overall pricing and market positioning of the footwear. Balance the desired material quality with your target price range.
Types of Insole Materials:
EVA (Ethylene-vinyl acetate): Lightweight, cushioning, and breathable, making it a popular and relatively inexpensive choice for various footwear types.
PU (Polyurethane): Durable, long-lasting, and supportive, with a wider range of hardness options available. Offers excellent shock absorption and abrasion resistance.
Cork: A renewable hard material that conforms to the shape of the wearer’s foot, providing support.
Memory Foam: Offers a custom-fit experience by conforming to the shape of the wearer’s foot, providing exceptional comfort.
Gel: Known for its soft and cushioning properties, gel insoles offer enhanced shock absorption and comfort.
TPU (Thermoplastic Polyurethane): A hard material used for structural support, stability, and alignment around the heel and arch. Ideal for orthotics and performance sport footwear.
Carbon Plate: Lightweight and durable, carbon plates provide excellent energy return and are commonly used in long-distance running shoes. However, they are more expensive.
Material Innovation:
In addition to traditional insole materials, innovative options are emerging in the market. These advancements enable designers to push boundaries and offer unique value to their customers.
3D Printing/Custom Scans: A niche segment of the insole market that allows for customized insole production based on individual foot scans. Note that this technology is currently limited in terms of scalability and cost-effectiveness.
Recycled Materials: Sustainable options are gaining popularity, utilizing recycled materials to create insoles with reduced environmental impact.
Bio-based Materials: Bio-based materials for insoles offer a sustainable alternative to traditional petroleum-based foams. These innovative materials can provide a responsible alternative to traditional petroleum-based foams commonly used in insoles. These materials are derived from renewable plant sources such as corn, mushrooms, cork, algae, and agricultural residues. Each bio-based material offers a unique set of features and sustainable benefits, depending on its chemical structure. Many of these materials are considered premium and novel technologies in the footwear industry. While some possess similar attributes to petrochemicals, they are designed to reduce environmental impact, making them an ideal choice for eco-conscious footwear.
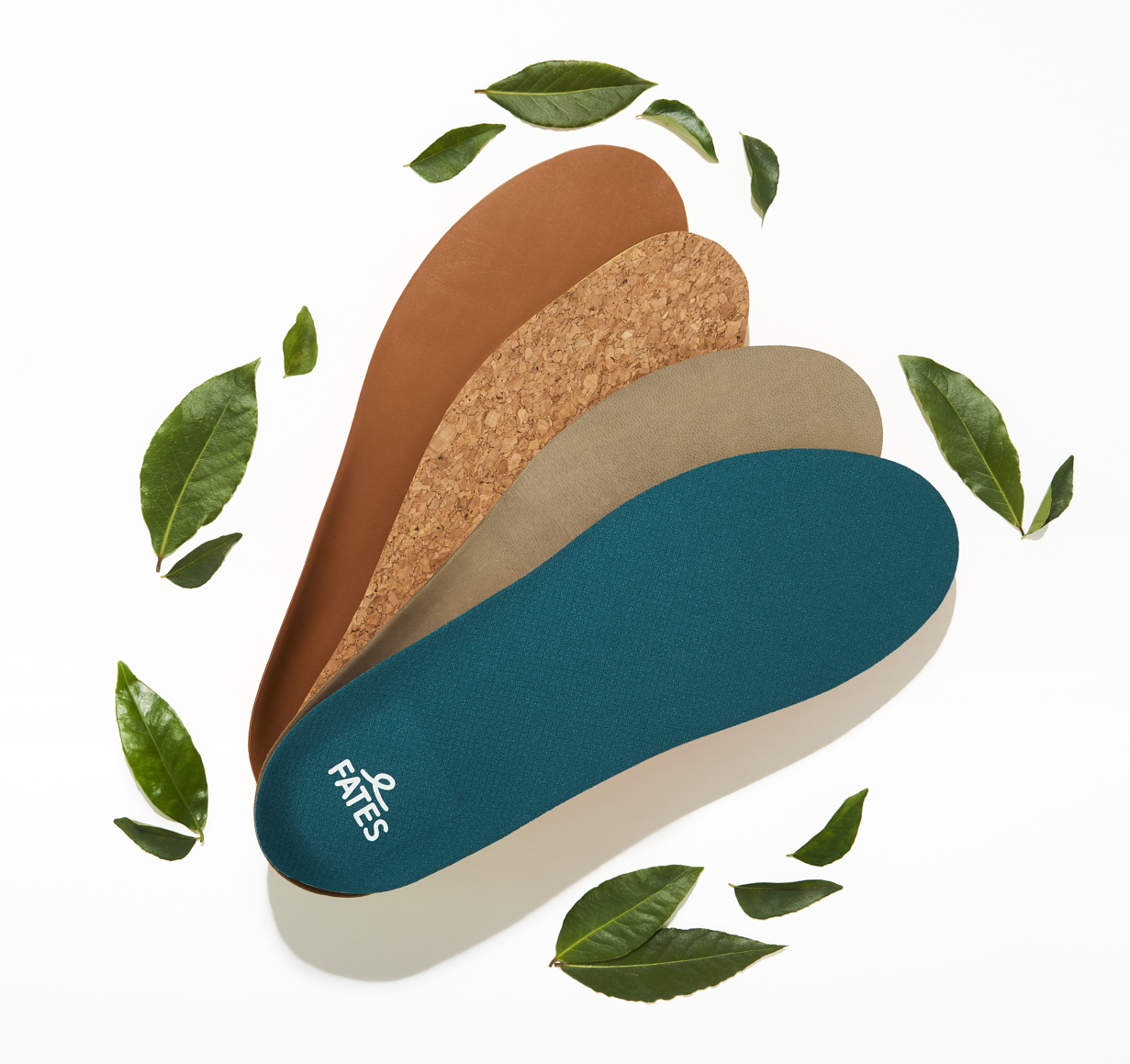
FATES bio-based foam has undergone rigorous third-party certification to ensure that its bio-content is derived solely from plant-based sources. With footwear designers in mind FATES bio-based foam has been developed for versatility, from poured PU, low density sheetstock for die cut or compression molding, bio-based memory foam and even TPU for insole projects.
Additionally, an extensive Life Cycle Analysis (LCA) has been conducted, confirming its measurably lower environmental impact compared to traditional polyurethane foam. FATES bio-based foam has been engineered to deliver high performance, with biodegradable properties ensuring minimal impact at end of life.
Choosing the right insole material is a crucial step in footwear design, impacting comfort, support, and overall customer satisfaction. By considering factors such as footwear type, activity level, material properties, and price point, designers can make informed decisions. Additionally, exploring material innovations like 3D printing, recycled materials, bio-based options.
Contact us to find your next material solution
FATES: The Raw Materials
FATES: The Raw Materials

The bioeconomy and its role in mitigating climate change
Measuring impact of sustainable practices is key to driving effective change. From fashion to furniture, from the clothes we wear to the cars we drive, producing consumer goods results in billions of tonnes of GHG (greenhouse gas) emissions – contributing to climate change. Globally the footwear industry produces 700 megatons of CO2eq of GHG emissions every year, up to 40% of the emissions are attributed to raw materials manufacturing and extraction.[1]
Part of the solution is transitioning to a plant or bio-based economy.
The bioeconomy can be defined as using renewable biobased resources sustainably to produce food, energy and goods. It allows industries to tap into biomass available from agricultural, forestry feedstocks and waste streams that are critical to achieving a net-zero, sustainable future.
The power of plants
Plants are one of the most abundant renewable resources on earth. Nature produces more plant matter in one day than the sum of all the petrochemistry-based materials produced globally per year.[2] Plant-based chemistry is comparable to petrochemicals without the negative impact, plants have emerged as a sustainable alternative such as coconut husk, ground stone fruit pits or lignin.
The impact of renewable plant-based materials on the environment is far less compared to oil-derived counterparts. By conducting a life cycle analysis, Evoco is able to measure the impact of its plant-based material technology, FATES®, from cradle to gate.
The results are clear, FATES® reduces GHG emissions at the source by up to 70%; using plant-based raw materials results in a substantial step change.
FATES® was designed to be feedstock agnostic and adapt to local plant feedstocks across the globe
FATES® is feedstock agnostic material technology, leveraging raw materials derived from a variety of plant by-products. The technology works with a variety of inputs from agricultural, forestry, by-products and waste. We can adapt to a variety of first and second feedstocks, depending on local supply chains.
Our feedstock today & regenerative farming
FATES® current feedstock includes field corn. Field corn widely available, and sustainably cultivated in the North American supply chain. Our raw material does not compete with the food supply. Our technology uses the low-calorie starch by-products leftover (something humans cannot consume) after the corn is processed for animal feed and human consumption. This Ensures that no potential food source or land is diverted to non-food requirements. Currently dedicated arable land for biopolymers is 0.015% and is estimated to increase to 0.058% in 2026. This figure is still less than 0.1% of total arable land and equates to 0.004% of the land use for food & feed.[3]
To put things in perspective, a quarter of food grown is discarded, if only one tenth was allocated to biopolymers, it would allow enough raw materials to replace all petrochemical based plastics.[4]
Our path tomorrow
Future feedstocks include biomass materials such as castor oil, nutshell oils and waste residue, lignin, and algae with further potential to use the 2nd generation agricultural wastes. With sustainability the end goal, life cycle analysis of other biomass feedstocks and waste show that there is no guarantee lower environmental impact because of added steps.
As technology advances, we will continue to monitor and quickly adapt to the most sustainable feedstock options available.
References
[1] Quantis. (2018). Measuring Fashion: 2018 Insights from the Environmental Impact of the Global Apparel and Footwear Industries study. Retrieved April 25, 2022, from https://quantis-intl.com/report/measuring-fashion-report/
[2] Lupton, M. (2017, May 24). Plant Matter Outweighs Petrochemicals as the Building Blocks for the Future. AZoCleantech.
[3] European Bioplastics (2021), FAO Stats (2020), nova-Institute (2021), and Institute for Bioplastics and Biocomposites (2019), University of Virginia (2016). Info: www.european-bioplastics.org
Contact us to find your next material solution
News
From Plants to Footwear: The Science Behind Plant-Based Polyurethane
From Plants to Footwear: The Science Behind Plant-Based Polyurethane

The history behind polyurethane
Polyurethane (PU) was discovered in the 1930s as an alternative to rubber, and is highly regarded for its durable, flexible, and chemical resistance properties.
In the 1950s, polyurethane foam (PU foam) was popularized and found in almost all aspects of our daily lives. From footwear, apparel, furniture, bedding, and automobiles, you are probably sitting on, sleeping on, driving in, or wearing PU foam.
How polyurethane foam is made
It starts with a few key chemicals mixed:
Polyols + Additives + Isocyanate = urethane bonds.
This reaction creates the polyurethane foam that we all love for its comfort and performance.
Today, PU foams can be made conventionally from oil-derived chemicals (petrochemistry) or from plants. Both oil and plant-based PU foams go through a similar production process, but it is the development and raw materials that make plant-based polyurethane foams more sustainable and allow for high performance properties.
Where conventional oil-based polyurethane foam comes from?
Simply put, oil-based PU is made from petrochemicals or fossil fuels, mainly crude oil. These non-renewable resources have a high impact on the environment and use toxic materials that pollute the soil and degrade into microplastics.
How bio-based polyurethane foam is disrupting the foam industry
FATES®, Evoco’s plant-based foam, starts by extracting glucose, starches, and other building blocks from plants. We harness the basic components from these plants and use them to develop plant-based chemistry, resulting in a diverse range of formulas that meet a wide variety of technical specifications such as density, tensile strength, elongation and more. FATES eco-foam is made from up to 80% plants, reducing GHGs (greenhouse gas) emission by up to 70% in comparison to conventional oi-based PU foam This positive environmental impact is substantiated by a third-party verified, cradle–to–gate LCA (Life Cycle Assessment) model. In addition, FATES does not use heavy metal catalysts, and is shown to degrade back into the earth, creating a circular material.
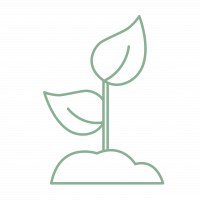
It starts with plants
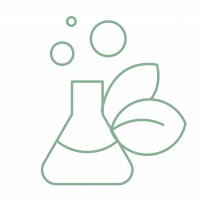
We harness the power of plants into chemistry
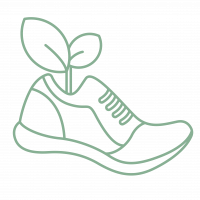
Using our chemistry, we develop plant-based materials used in footwear and more
How bio-based polyurethane foam can push innovation in the footwear industry
PU foam is widely used in footwear for its desirable properties of cushioning and shock-absorbing properties, flexibility, and its ability to be a completely customizable component. Our team of scientists and engineers have developed patented formulations to enhance PU foam properties and create a high-performing sustainable alternative.
As more deliverables and constraints are set into footwear development such as performance, sustainability, supply chain integration and consumer expectations, our bio-based chemistry platform allows to integrate these various factors to design the perfect material formulation for any footwear project.
As the footwear industry adapts to consumers expanding their interest in sustainable features and benefits, FATES plant-based foam allows for a seamless, high performance, low impact solution.